|
Method no.: |
ID-214 |
|
|
Matrix: |
Air |
|
|
OSHA Permissible
Limits Final Rule Limits: |
|
|
|
Time
Weighted Average (TWA): |
0.1
ppm * |
|
|
Short-Term
Exposure Limit (STEL): |
0.3
ppm * |
|
|
Transitional Limit (TWA): |
0.1 ppm |
|
|
Collection
Device: |
An air
sample is collected using a calibrated sampling pump and a
two-piece polystyrene cassette containing two
nitrite-impregnated glass fiber filters (IGFFs). During
collection, ozone reacts with the nitrite impregnated on the filter
collection device and converts it to nitrate via oxidation. |
|
|
Recommended
Sampling Rate (See Special Precautions below) TWA: TWA: |
0.25 to
0.5 liter per minute (L/min) 1.5 L/min |
|
|
Recommended Air Volume |
|
TWA: |
90 L (180 min at
0.5 L/min). Longer sampling times can be used (up to 480 min) when
using 0.25 L/min flow rate. |
STEL: |
22.5 L (1.5 L/min
for 15 min) |
|
|
Analytical
Procedure: |
The reaction
product is extracted from the filters and blanks using deionized
water and the extracts are analyzed by ion chromatography as nitrate
using UV-VIS detector at 200 nm wavelength. A
conductivity detector can also be used. |
|
|
Detection
Limit
Qualitative:
Qualitative: |
0.008
ppm (90-L air sample) 0.032 ppm (22.5-L air sample) 0.03 ppm
(90-L air sample) 0.11 ppm (22.5-L air sample) |
|
|
Accuracy |
TWA |
STEL |
Validated Range: |
0.070 t 0.224
ppm |
0.330 ppm |
CVT(pooled): |
0.045 |
0.054
(CV2 |
Bias: |
+0.014 |
-0.015 |
Overall Error: |
±10.4% |
±12.3% |
|
|
Method Classification: |
Validated
Method |
|
|
Special
Precautions: |
Slight
breakthrough (~7.5%) of ozone was noted at approximately 0.4 ppm. If
the expected ozone (O3) concentration is more than 0.2
ppm, the recommended sampling rate can be reduced to 0.25
L/min. |
|
|
Date: March 1995 |
Chemist: James C. Ku |
|
|
* The U.S.
Court of Appeals, Eleventh Circuit, has ruled that Final Rule Limits
of 29 CFR 1910.1000 be vacated. The Final Rule definition of "TWA"
and "STEL" have been retained. Although the Final Rule Limits have
been vacated, OSHA encourages industry and government to abide by
these limits established by scientific evidence (memorandum for
Directorate Heads, Office Directors and Regional Administrator from
Roger Clark, Director of Compliance Programs OSHA, 3/30/93). |
|
|
Commercial manufactures and products mentioned in this
method are for descriptive use only and do not constitute
endorsements by
USDOL/OSHA.
Similar products from
other sources can be substituted.
|
Branch of Inorganic Methods Development OSHA Salt Lake
Technical Center Sandy, Utah
|
1.
Introduction
This method describes the sample collection and
analysis of airborne ozone (O3). Air samples are taken in
the breathing zone of workplace personnel, and analysis is performed
by ion chromatography (IC) equipped with a UV-VIS and
conductivity detector. Nitrate analysis by conductivity is well
established since the 1970s. Both UV-VIS and
conductivity detectors are suggested in this method to allow
versatility and offer the possibility of excluding interferences by
switching detectors. This method is not applicable for collection
and analysis of bulk or wipe samples.
1.1 History
Many previous attempts were made to
measure ozone in occupational environments. All have various
shortcomings and demonstrate the past degree of difficulty in
developing an adequate method. A chronological presentation of
some of the methods OSHA has used or evaluated is discussed below:
1.1.1 Detector tubes: The major drawback of detector
tubes is the need to use a cumbersome statistical technique to
assess Time Weighted Average (TWA) exposures.
1.1.2 KI
and AKI methods: An early method to determine occupational
exposure to ozone in the workplace involved collection in
neutral potassium iodide (KI) solution and analysis by
colorimetry (Ref.
5.1). A modification involved collecting samples in an
alkaline potassium iodide (AKI) solution and analyzing them by
colorimetry after acidifying with sulfamic acid (Ref.
5.2). It has been reported (Ref.
5.3) that the reaction of ozone with AKI to produce iodine
is not quantitative and is concentration dependent. Therefore, a
conversion equation must be used to convert the values
equivalent to the neutral KI method.
1.1.3 OSHA KIBRT
(potassium iodide-potassium bromide-sodium thiosulfate) (Ref.
5.4): This method resolved some of the stability and
interference problems associated with prior methods which used
KI.
1.1.4 Trans-stilbene (Ref.
5.5): Previous work has been reported using glass beads
coated with trans-stilbene for collecting ozone (Ref.
5.6). Preliminary tests showed that this method was affected
by humidity as low as 50 % relative humidity (RH) (Ref.
5.7). To compensate for this humidity problem, an impinger
sampling method using a collection solution (as stated in
chronological list below) was developed at the
OSHA-SLTC (Ref.
5.5). Although this method could be used under controlled
conditions as a reference method in the laboratory, the 90%
acetonitrile in water is flammable and should not be used for
field use. Alternative non-flammable collection
solutions were not found during this study.
1.1.5
Direct-Readers AID Model 560 (Ref.
5.8) or AED-030 (
Ref. 5.9): A strip chart recorder to record data was used to
document for both direct-readers compliance monitoring. The AID
Model 560 also required a battery recharge every 8 to 10 hours,
making it inconvenient. The AED-030 can be used for
only 4 to 5 hours with batteries; a line voltage power converter
or replacement batteries is necessary for longer
periods.
1.1.6 Recently, it has been reported (Ref.
5.10) that the measurement of ozone can be done using a
commercially available passive sampling device containing a
nitrite-impregnated filter. According to the
manufacturer, the shelf-life of the sampling
portion of the passive device is conservatively 4 weeks from the
nitrite impregnation date to the analysis date. Based on the
nitrite principle, OSHA Method ID-214 was developed
as an active sampling system. The commercially available passive
system was initially tested and some of the data is included in
the backup report (Section
4.) Because of sensitivity (Section
4.10) and potential interference considerations of the
passive sampler, this active sampling method is more suitable
for OSHA compliance purposes.
A chronological summary of
OSHA SLTC ozone monitoring techniques is shown below:
Date |
Method |
Principle |
Collection Medium |
Major Advantages |
Major
Disadvantages |
1960s - present |
Detector tubes |
Oxidation of indigo by
ozone resulting in white color |
Direct-read |
Simple, rapid |
Interferences, more a
spot check for exposure measurement |
Before 1977 |
1% Neutral buffered
KI |
Reaction with KI |
1% KI, phosphate
buffer, pH=6.8 |
Simple, rapid, and
sensitive |
Bubbler, unstable, and
interferences from all oxidants |
1977 - 80 |
Alkaline KI |
Reaction with KI |
1% KI, 1.0 N NaOH,
pH>11 |
Simple, rapid, and
sensitive |
Bubbler, unstable,
sampling rate dependence, and interferences from all
oxidants |
1983 - 92 |
Ozone meter (AID Model
560) |
Chemilumines- ence |
Direct reading
instrument |
Very sensitive,
direct-reading, very specific |
No data logging and
bulky instrument requiring ethylene (flammable gas) or
Ethychem (ethylene in CO2) |
1986 |
Neutral buffered
(KIBRT) |
Reaction with KI and
Na2S2O3. Measurement of
excess I2 |
1% KI, a known amount
of thiosulfate, 2% KBr |
Simple, rapid
sensitive, stable and some independence from sampling rate |
Bubbler, interferences
from all oxidants. Potential contam- ination. |
1990 - 91 (Lab use
only) |
Glass beads
trans-stilbene |
Reaction with
olefins |
Glass beads coated
with trans-stilbene |
Simple, rapid,
sensitive and O3 specific |
Recovery dependent on
humidity |
1990 - 91 (Lab use
only) |
trans-stilbene and
mesitol |
Reaction with
olefins |
0.05% trans-stilbene +
0.5% mesitol in a mixture of acetonitrile/ water (9:1) |
Simple, rapid,
sensitive and O3 specific |
Flammable liquid,
bubbler used for sample collection |
1992 - present |
Ozone meter
(AED-030) |
Semi-conductor
sensor |
Direct reading
instrument |
Simple, rapid,
sensitive and easy to use |
No data logging
capacity, instrument treads to drift |
This method |
IGFF |
Reaction with
nitrite |
Nitrite-coated
IGFFs |
Simple, rapid,
sensitive |
Interference from
SO2 |
1.2 Principle
Ozone is
collected using two nitrite-impregnated glass fiber filters
(IGFFs). The second IGFF serves as a backup filter. The collected
O3 converts nitrite (NO2¯) to nitrate
(NO3¯) via oxidation as shown by the following chemical
reaction:
NO2¯
+ O3
NO3¯ + O2 | The resultant NO3¯ is analyzed by IC
using a UV-VIS detector at a wavelength of 200 nm. A gravimetric
conversation factor is used to calculate the amount of
O3 collected from the amount of NO3¯
found.
1.3 Advantages and Disadvantages
1.3.1 This method has adequate sensitivity for
determining compliance with the OSHA Permissible Exposure Limit
(PEL) of 0.1 ppm for O3 exposure. The method is also
capable of monitoring Food and Drug Administration limit of 0.05
ppm O3 in enclosed spaces (21 CFR 801.415). The U.S.
Environmental Protection Agency (EPA) has established a National
Ambient Air Quality Standard (NAAQS) for O3 at 0.12
ppm for a 1-hour average. The method is capable of monitoring
for the EPA limit provided a sampling rate of at least 0.5 L/min
is used. All three limits have been used to determine Indoor Air
Quality (IAQ) in relation to O3
exposure.
1.3.2 The method is simple, rapid, and easily
automated.
1.3.3 The method is "relatively" specific for
O3 (as NO3¯) in the presence of other
nitrogen-containing substances, such as nitrogen
dioxide (NO2).
1.3.4 The sampling device is
small, portable, and contains no liquid.
1.3.5 Desorption
and preparation of samples for analyses involve simple
procedures and equipment.
1.3.6 Samples can be analyzed
using either a UV-VIS or conductivity detector. The majority of
the validation was performed using a UV-VIS
detector.
1.3.7 One disadvantage is that sulfur dioxide
(SO2) gas and soluble particulate nitrate compounds
interfere when collected on the same IGFFs (Section
4.9). A pretube containing a chromate compound can be used
to remove any SO2 and allow O3 to react
with the IGFFs. Significant levels of soluble nitrate substances
should not normally be encountered in an occupational setting
unless these substances are in use. Examples of soluble
substances are potassium or sodium nitrate.
1.3.8 Another
disadvantage of the method is the tedious preparation and
storage of the IGFFs (Section
2.1.3). 1.4 Methods Performance
A synopsis
of the method performance is presented below. Further information
can be found in Section
4.
1.4.1 This method was validated over the
concentration range of 0.070 to 0.224 ppm. An air volume of 90 L
and a flow rate of 0.5 L/min were used.
1.4.2 The
qualitative detection limit was 0.37 µg/mL or 1.85 µg (as
NO3¯) when using a 5-mL solution volume.
This corresponds to 0.008 ppm O3 for a
90-L air volume.
1.4.3 The quantitative
detection limit was 1.25 µg/mL or 6.25 µg (as NO3¯)
when using a 5-mL solution volume. This corresponds
to 0.03 ppm O3 for a 90-L air volume. A 50-µL sample
loop and a detector setting of 2 absorbance units (AU) for
full-scale output were used.
1.4.4 The sensitivity of the
analytical method, when using the instrument parameters listed
in Section
3.6.3, was calculated from the slope of a linear working
range curve (0.5 to 10.0 µg/mL NO3¯). The sensitivity
was 3.7 × 105 area units per 1 µg/mL. A Dionex Series
4500i ion chromatograph with a Linear UVIS-206 UV
detector and AI450 computer software was used (Dionex,
Sunnyvale, CA).
|
TWA |
STEL |
CV |
0.045 |
0.054 |
Bias |
+0.014 |
-0.015 |
OE |
±10.4% |
±12.3%
| 1.4.5
The total pooled coefficient of variation (CV), bias, and total
overall error (OE) for TWA and STEL-type
determinations are shown below:
1.4.6 The collection
efficiency at 2 times the PEL was 100%. Samples were collected
from a generated test atmosphere of 0.20 ppm O3 for
180 min at 0.5 L/min.
1.4.7 For TWA measurements, two
breakthrough tests were performed at concentrations of 0.22 and
0.4 ppm O3. Using a sampling time of 240 min and an
average sample flow rate of 0.5 L/min, no breakthrough was found
at a concentration of 0.22 ppm O3, and the average
breakthrough was 7.5% at a concentration of 0.4 ppm
O3. However, no breakthrough was found at a
concentration of 0.6 ppm O3 after reducing the flow
rate to approximately 0.25 L/min and a sampling time of 240 min.
For STEL, no breakthrough was found at a concentration of 0.33
ppm O3 using a sampling time of 15 min and an average
sample flow rate of 1.5 L/min.
1.4.8 Samples can be
stored at ambient (20 to 25°C) temperature for a period of 30
days. Results show the mean sample recovery after 30 days
storage was within ±10% of results at Day 0.
1.4.9 The
mean blank recovery after 30 days storage was 5 µg compared to
1.5 µg on Day 0 (as total nitrate). A final solution volume of 5
mL was used. 1.5
Interferences
1.5.1 Sampling: Because O3 is analyzed as
nitrate, particulate nitrate compounds may interfere (positive)
in the analysis if collected on the same IGFFs. Sulfur dioxide
in the presence of O3 will also interfere (negative).
If interference from SO2 is expected, an oxidizer
pretube, such as the tube commonly used for converting NO to
NO2 (OSHA Method ID-182
or ID-190),
can be used to effectively remove SO2 and allow
O3 to pass through the IGFFs. These oxidizer tubes
must be passivated in the ozone atmosphere prior to
use.
1.5.2 Analytical: Any substance that absorbs UV at
20 nm and has the same retention time as NO3¯ is an
interference when using the UV-VIS detector. If the
possibility of an interference exists, changing the analytical
conditions (detector settings, chromatographic column, eluent
flow rate, strength, etc.) may circumvent the problem.
Substances that have the same retention time as NO3¯
and are conductive may interfere when analyzed by conductivity.
Most interferences may be resolved by changing detectors (i.e.,
changing from conductivity to UV-VIS or
vice-versa). 1.6 Industrial Uses and
Products of Ozone (Ref.
5.11)
1.6.1 Ozone is used mainly for: purification of
drinking water; industrial waste treatment; deodorization of air
and sewage gases; bleaching of waxes, oils, wet paper, and
textile; production of peroxides; and as a
bactericide.
1.6.2 Ozone is also used as: an oxidizing
agent in several chemical processes (acids, aldehydes, and
ketones from unsaturated fatty acids); steroid hormone
formation; removal of chlorine from nitric acid; and oxidation
of phenols and cyanides. 1.7 Physical and Chemical
Properties (Refs. 5.11-5.12)
Ozone
has a pungent odor, is a strong irritant, and is highly toxic by
inhalation. It is strong oxidizing agent and a dangerous fire and
explosion risk when in contact with organic materials. It is more
soluble in water than oxygen; however, the minimal solubility
results in the liberation of significant amounts of ozone after
water is purified with ozone.
CAS No. |
10028-15-6 |
Chemical formula |
O3 |
Formula weight |
47.997 |
Specific gravity |
1.6 (liquid) @ -183°C |
Melting point |
-192°C |
Boiling point |
-112°C |
Vapor density (air = 1) |
1.65 |
Synonym |
Triatomic oxygen |
Appearance and odor |
Colorless at concentrations noted in
industry. Pungent characteristic odor usually associated
with electric sparks. | 1.8 Toxicology (Ref.
5.13)
Information listed within this section is a synopsis of
current knowledge of the physiological effects of O3
and is not intended to be used as a basis for OSHA
policy.
Ozone is highly injurious and potentially lethal to
experimental animals at concentrations as low as a few parts per
million (ppm). A study in which young mice were exposed to 1 ppm
ozone for 1 or 2 days reported damage to alveolar tissue. Human
populations chronically exposed to lower concentrations of ozone
were observed to have adverse changes in lung function. Human
volunteers exposed to 0.5 ppm ozone for 3 hours per day, 6 days
per week, for 12 weeks showed significant adverse changes in lung
function. Another report showed a 20 percent reduction in timed
vital lung capacity in persons exposed to average concentrations
of ozone of 1.5 ppm for 2 hours. Welders exposed to maximal ozone
concentrations of 9 ppm were observed to have pulmonary
congestion. Recent studies indicate ozone may contribute to
inflammation in human bronchial tubes. Further information
regarding toxic effects of ozone can be found in Ref.
5.12. 2.
Sampling
Note: Particulate nitrate compounds or SO2, gas
interfere in the analysis of NO3¯ if collected on the
same IGFFs. However, if interference from SO2 is
expected, a pretube, such as the tube used for converting NO to
NO2, can be used to effectively remove SO2,
and allow O3 to pass through to the IGFFs. If the amount
of SO2 in the area to be sampled is unknown, detector
tubes (OSHA SLTC Product Evaluation No. 12 for recommended tubes)
can be used to screen the area or a long-term sampling
method (OSHA SLTC Method ID-200)
can be used to determine if SO2 is present prior to
O3 sampling. If particulate nitrate compounds are present
in the air, contact OSHA-SLTC. If these compounds are
soluble and present in sufficient quantity, an alternate method
employing direct-reading instruments may have to be
used.
2.1 Equipment
2.1.1 Calibrated personal sampling pumps capable of
sampling within ±5% of the recommended flow rate of 0.5 L/min
are used.
2.1.2 Tygon or other flexible tubing for
connecting pumps to samples.
2.1.3 Sampling
media:
Impregnated glass fiber filters (IGFFs) are
used for sample collection and are obtained from
OSHA-SLTC for OSHA use. The filters can also be
prepared as explained below:
Note: Before impregnation, glass fiber filters (GFFs) must be
thoroughly cleaned with deionized water (DI H2O to remove
any trace amounts of soluble nitrate compounds. Filter impregnation
requires the use of very pure chemicals, and careful handling of
both the chemicals and IGFFs is required to avoid contamination from
soluble nitrate-containing substances. After preparation, the IGFFs
must be stored in clean cassettes and sealed with scaling bands
before use. A conservative shelf-life of 4 weeks should
be observed.
- Glass fiber filters (GFFs), 37-mm (Prod. no. 61652, Type
A/E, 500/pkg, Gelman Sciences, Ann Arbor, MI)
- Glass beakers, 400 - 500-mL and 10 - 15-mL (or 25-mL
Erlenmeyer flasks)
- Oven, 0 - 200°C
- Forceps
- Cassette gel sealing bands
- Plastic end plugs
- Two-section polystyrene cassettes, 37-mm diameter (part
no. MAWP037 AO, Millipore Corp., Bedford, MA)
- Principal chemicals - These should be
at least reagent grade or better to avoid nitrate
contamination:
Sodium nitrite (NaNO2),
97+% Potassium carbonate (KCO3),
99% Glycerol, 99.5%
Impregnated glass fiber filters (IGFFs) are
prepared by chemically treating 37-mm GFFs according to the
following procedure:
- Prepare an "impregnating solution" by adding 0.3 g
NaNO2, 0.28 g K2CO3,and 1 mL
of glycerol to 100 mL DI H2O.
- Clean approximately 100 GFFs thoroughly by carefully
placing the filters using forceps into a thoroughly cleaned
beaker (1- or 2-L) with approximately 400-500 mL DI
H2O. Decant and rinse by adding another 400 to 500
mL DI H2O. Decant, and then dry the filters in the
oven at 100°C for 60 min or until completely dry.
- Set each GFF on the top of a 10-mL beaker or a 25-mL
Erlenmeyer flask.
- Slowly spike 0.4 mL of impregnating solution on each GFF
making sure the entire filter is saturated.
- Carefully place each beaker or Erlenmeyer flask (on which
each IGFF is sitting) into an oven and dry at 100°C for 30
min.
- Carefully and slowly remove all beakers or Erlenmeyer
flasks from the oven and allow to cool to room temperature.
(Note: Do not allow the filters to stand once they have cooled
to room temperature and prior to placement in cassettes. They
will react with any atmospheric ozone present.) Using forceps,
immediately place two IGFFs into a clean cassette, seal with
plastic end plugs, place a shrinkable gel band around each
cassette, and record the date. (Note: The sides of the IGFF
have different textures. One side is rough, the other is woven
and has a waffle-like appearance. Make sure the
rough sides of two IGFFs are face up, i.e., facing the
incoming sample.)
- IGFFs prepared in this fashion are stable for at least 28
days (Section
4.10).
2.1.4 A stopwatch
and bubble tube or meter to calibrate pumps.
2.1.5
Various lengths of polyvinyl chloride (PVC) tubing to connect
sampling tubes to pumps.
2.1.6 Oxidizer tube for removing
SO2 in the sampled air.
If there is reason to suspect the sampled
air could contain SO2, an oxidizer tube must be used to
remove the SO2. See Figure 1 below and also Section
4.9 for further details.
Oxidizer tubes normally used to
convert nitric oxide to nitrogen dioxide will suffice; however,
the contents of the tubes must be passivated with O3
prior to use. Oxidizer tubes can be obtained from SKC Inc.,
Eighty Four, PA as a Special Order item. The manufacturer or the
user can passivate the oxidizer tubes prior to use, and a
shelf-life after passivation of one to two years
should be observed. Passivation requires special
ozone-generating equipment. Oxidizer tubes and any
Tygon tubing used in sampling must be conditioned with ozone
using the following procedure (Note: The O3
generation system used to validate this method and condition the
oxidizer tubes and Tygon tubing is further discussed in Section
4.2.1. Other comparable systems can be used.):
- Connect one end of each open oxidizer tube to the ozone
generation system with short pieces of Tygon tubing. (Note
that this tubing will also be passivated and should be used as
the oxidizer-cassette connector when taking a
sample using an oxidizer tube.)
- Set the O3 concentration for the generation
system at approximately 0.1 ppm.
- Set the sampling pumps at approximately 0.5 L/min flow
rates. Connect the other end of the open oxidizer tube to each
sampling pump using Tygon tubing.
- Condition the oxidizer tubes for 4 h. Stop the sampling
pumps and cap the tubes using plastic caps or flame seal. The
shelf-life of the oxidizer should be 1 to 2
years.
2.2 Sampling
Procedure
2.2.1 Remove both plastic end plugs from the
cassette and connect the cassette to the calibrated sampling
pump, making sure the sampled air enters the rough side of the
IGFF. Use an oxidizer tube only if SO2 is suspected
of being present in the sampled air (Figure 1). Place the
sampling device on the employee such that air is sampled from
the breathing zone.
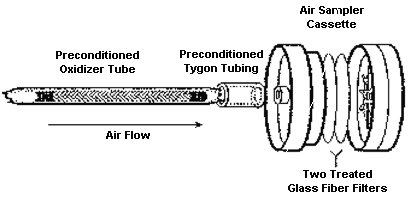 Figure 1.
Ozone sampler with oxidizer
tube. | 2.2.2 Use
a flow rate of 0.5 L/min and a sampling time of 180 min. Take
additional samples as necessary. A 0.25 L/min flow rate and a
sampling time up to 480 min can also be used.
2.2.3 After
sampling, immediately replace both plastic end plugs tightly in
the cassette and apply OSHA Form 21 seals in such a way as to
secure the end plugs.
2.2.4 Record the sampling
conditions such as sampling time, air volume, flow rate, etc. on
the OSHA 91A. When other compounds are known or suspected to be
present in the air, record such information and transmit with
the samples.
2.2.5 Handle a blank filter and cassette in
exactly the same manner as the sample cassettes except that no
air is drawn through it. Use the same lot and preparation date
of IGFF/cassettes for blank and collected samples. Prepare at
least one blank filter and cassette for each batch of ten
samples.
2.2.6 Send the samples and blanks to the
laboratory as soon as possible with the OSHA 91A paperwork
requesting ozone analysis. 3. Analysis
3.1 Safety Precautions
3.1.1 Review appropriate IC instrument manuals,
UV-VIS detector or spectral array detector maintenance manual,
and the Standard Operating Procedure (SOP) for proper instrument
operation (Ref.
5.14).
Note: The SOP is a written procedure for a specific instrument.
It is suggested that SOPs be prepared for each type of instrument
used in a lab to enhance safe and effective operation.
3.1.2 Observe laboratory safety regulations and
practices.
3.1.3. Review any MSDSs provided with reagents
and samples. Observe all precautions. Many chemicals are
hazardous. Use appropriate personal protective equipment such as
safety glasses, goggles, face shields, gloves, and lab coat when
handling these chemicals. 3.2
Equipment
3.2.1 Ion chromatograph (Model 4000i or 4500i
Dionex, Sunnyvale, CA) equipped with a UV-VIS
detector (Linear UVIS-206, Multiple wavelength
detector, Linear Instruments Corporation, Reno, NV) or a
conductivity detector.
3.2.2 Automatic sampler (Dionex
Model AS-1) and 0.5-mL sample vials/caps (Dionex part no.
38011).
3.2.3 Laboratory automation system: Ion
chromatograph interfaced with a data reduction system (AI450,
Dionex).
3.2.4 Separator and guard columns, anion (Model
HPIC-AS9 and AG9, Dionex).
3.2.5 Forceps.
3.2.6
Disposable beakers (10 and 50 mL).
3.2.7 Cassette opener
(SKC E-Z Opener, Cat. No. 225-13-5, SKC) or similar tool such as
a coin or a screwdriver.
3.2.8 Disposable syringes (1
mL).
3.2.9 Syringe prefilters, 0.5-µm pore size (part no.
SLSR 025 NS, Millipore Corp.,Bedford, MA).
Note: Some syringe prefilters are not cation- or anion-free.
Blank reagent solutions should be filtered and analyzed first to
determine potential contamination and suitability with the
analyte.
3.2.10 Miscellaneous volumetric glassware: Pipettes,
volumetric flasks, Erlenmeyer flasks, graduated cylinders, and
beakers.
3.2.11 Equipment for eIuent degassing (vacuum
pump, ultrasonic bath).
3.2.12 Analytical balance (0.01
mg).
3.2.13 Scintillation vials, 20 mL, with
polypropylene- or Teflon-lined caps.
3.2.14 Treated glass fiber filters (IGFFs from
Section
2.1.3) for spiking or matrix matching (if necessary).
3.3 Reagents - All chemicals should be at least reagent grade.
3.3.1 Principal reagents:
Sodium carbonate
(Na2CO3), 99% Sodium bicarbonate
(NaHCO3), 99% Sodium nitrate (NaNO3),
99.9% Deionized water (DI H2O)
3.3.2 Eluent
(1.0 mM Na2CO3 + 1.0 mM
NaHCO3):
Dissolve 0.424 g
Na2CO3 and 0.336 g NaHCO3 in
4.0 L DI H2O. Sonicate this solution and degas under
vacuum for 15 min.
Nitrate (NO3¯) stock
standard (1,000 µg/mL):
Dissolve and dilute 1.3710 g of
NaN03 to 1.0 L with DI H20. Prepare every
6 months.
Note: The laboratory should have an
effective, independent quality control (QC) program in place and QC
samples of the analyte should be routinely analyzed along with field
samples. Depending on the capabilities of the program, QC samples
can either be generated using the collection media and substance
(O3) under controlled conditions, or media can be spiked
with the analyte (NO3¯). lf QC samples are not routinely
prepared and analyzed, two different standard stock solutions should
always be prepared and these solutions should routinely be compared
to each other. Always prepare the stocks from two different sources
or, as last resort, from different lots.
3.3.4 Nitrate
(N03¯) standard solutions, 100, 10, and 1 µg/mL:
Pipette appropriate volumes of the 1,000 µg/mL as
NO3¯ stock standard into volumetric flasks and dilute
to the mark with eluent. Prepare monthly.
3.4 Working Standard Preparation
- Prepare fresh prior to beginning the analysis.
3.4.1 Prepare NO3¯
working standards in eluent. A suggested scheme for preparing a
series of working standards using 10-mL final solution volumes
is shown below:
working std (µg/mL) |
std solution (µg/mL) |
aliquot (mL) |
eluent added (mL) |
0.5 1.0
* 2.0 5.0 10.0 |
1.0
1.0 10.0 10.0 10.0 |
5.0 - 2.0 5.0 - |
5.0 - 8.0 5.0 - |
* Already
prepared in Section
3.3.4 | 3.4.2
To prepare each working standard (Working Std) listed above,
transfer an appropriate amount of the Std Solution to a
disposable beaker, pipette an appropriate aliquot (Aliquot) of
the specified standard solution (prepared in Section
3.3.4) from the disposable beaker to an appropriate
container (scintillation vial, Erlenmeyer flask, etc.). Add the
specified amount of eluent (Eluent Added).
3.4.3 As an
alternative, pipette each aliquot into a 10-mL volumetric flask
and dilute to volume with eluent. 3.5 Sample Preparation
3.5.1 Carefully open each cassette with a cassette
opener (or similar tool, such as a coin or a screwdriver),
remove each IGFF and transfer each filter using a clean forceps
into separate 20-mL scintillation vials.
3.5.2 Pipette 5.0 mL of DI H2O into
each vial. Make sure the filter is wetted. Cap the vials using
polyethylene-lined plastic caps.
Note: Alternate desorption volumes can be
used and are dependent on the analytical sensitivity desired. For
most industrial hygiene samples, 5-mL volumes will allow for
analysis of ozone (as NO3¯) within the range of the
standards specified.
3.5.3 Allow the samples to sit
for at least 15 min. Occasionally swirl each
solution.
3.5.4 If the sample solutions contain
particulate, remove the particles using a prefilter and syringe.
3.6 Analysis
It is
imperative that the large nitrite peak (from the sampling media)
is adequately separated from the nitrate peak. This can be assured
by desorbing an IGFF (Section
3.2.14) with eluent, spiking the solution with a known amount
of nitrate working standard, and analyzing this solution prior to
analysis. The chromatogram shown below (Comparison of a Standard
and a Sample) demonstrates the peaks obtainable from a sample and
a standard without any matrix-matching. Peak
characteristics of the nitrate in the standard and sample are
similar, retention times appear very close, and there is adequate
separation of nitrite and nitrate. If a comparison of a spiked
sample and a nitrate standard indicates poor separation or
significantly different NO3¯ retention times,
matrix-matching or a change in analytical conditions
should occur. A new column could be used or the eluent strength
may be changed to facilitate separation. If
matrix-matching of standards and samples is the only
alternative, standards should be prepared with treated filters in
the same fashion as samples.
Comparison
of a Standard and a Sample
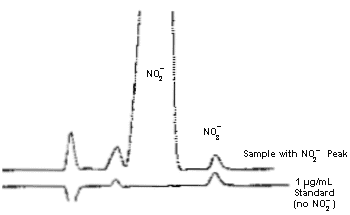 |
Text Version: This
figure shows a sample chromatogram superimposed over a
standard chromatogram. The sample chromatogram shows the
chromatographic separation of the nitrite peak from the
nitrate peak in a sample. The retention times for the
nitrate peak in the sample and the nitrate peak in the
standard are almost identical and show that the separation
of nitrite and nitrate is adequate. |
3.6.1 Pipette or pour a 0.5- to
0.6-mL portion of each standard or sample into separate
automatic sampler vials. Place a filtercap into each vial. The
large filter portion of the cap should face the
solution.
3.6.2 Load the automatic sampler with labeled
samples, standards, and blanks.
3.6.3
Set up the ion chromatograph in accordance with the SOP (Ref.
5.14). Typical operating conditions for a Dionex 4000i or
4500i with a UV-VIS detector (Spectral Array
detector) and an automated sampler are listed below:
Ion
chromatograph with UV detector * at 200 nm
wavelength
Eluent: |
1.0 mM NaCO3/1.0 mM
NaHCO3 |
Column temperature: |
ambient |
Anion precolumn: |
AG9 |
Anion separator column: |
AS9 |
Output range: |
2 absorbance units full scale
(AUFS) |
Rise time: |
5 sec |
Sample injection loop: |
50 uL |
|
|
Pump |
|
|
|
Pump pressure: |
~900 psi |
Flow rate: |
2 mL/min |
|
|
Chromatogram |
|
|
|
Run time: |
5 min |
Peak retention time: |
~3.00 min for
NO3¯ | * For detection using a conductivity detector,
output range and rise time are not used. A sensitivity setting
on the conductivity detector of 0.1 µS is used. All other
settings are similar.
Soluble nitrate compounds can
interfere when using either UV or conductivity detector.
Response to nitrate using either detector is similar and appears
to be dependent on column conditions, eluent strength, and
sensitivity settings.
3.6.4 Analyze samples, standards,
and blanks according to SOP (Ref.
5.14). 3.7
Calculations
3.7.1 After the analysis is
completed, retrieve the peak areas or heights. Obtain hard
copies of chromatograms from a printer. A chromatogram of a
sample collected at an ozone concentration of approximately 2
times the PEL for 180 min is shown below:
ret time |
component name |
concentration |
height |
area |
3.22 |
nitrate |
6.142 µg/mL |
218782 |
2202892 |
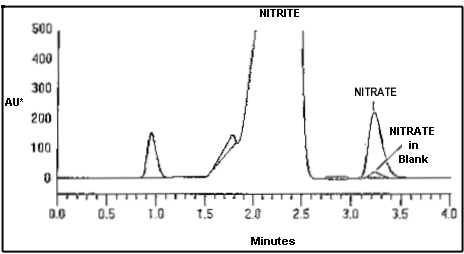 |
Text Version: This figure shows a
sample chromatogram superimposed over a blank sample
chromatogram. The sample chromatogram represents nitrate
from an ozone concentration of approximately two times the
PEL for a 180 min sample. The nitrate normally
occurring in a blank sample is shown for illustrative
purposes. Detector response and column retention
times were obtained using equipment and analytical
conditions specified in this
method. | *
Relative absorbance units using a UV-VIS detector
Note: The nitrate normally contained in a
blank is only shown for illustration purposes. Peak heights, peak
area, and retention times are instrument dependent and were obtained
using equipment specified in Section
3.2.
3.7.2 Prepare a
concentration-response curve by plotting the peak areas or peak
heights versus the concentration of the NO3¯
standards in µg/mL.
3.7.3 Determine total µg for each
sample and blank. Perform a blank correction for each IGFF.
Subtract the total µg blank value from each total µg sample
value.
Ab
= (µg/mL NO3¯)b × (Sol
Vol)b × (CF)
As = (µg/mL
NO3¯)s × (Sol Vol)s ×
(CF)
A = As -
Ab |
Then calculate the air concentration of
O3 (in ppm) for each air sample:
ppm O3 = |
A × (Mol Vol)
AV × (Mol Wt) |
where: |
|
|
Ab |
= |
Total µg O3 in blank |
As |
= |
Total µg O3 in sample |
A |
= |
µg O3 after blank
correction |
(µg/mL
NO3¯)b |
= |
Amount found (from calibration curve)
in blank |
(µg/mL
NO3¯)s |
= |
Amount found (from calibration curve)
in sample |
(Sol Vol)b |
= |
Blank solution volume (mL) from Section
3.5.2 (normally 5 mL) |
(SoI Vol)s |
= |
Sample solution volume (mL) from Section
3.5.2 (normally 5 mL) |
CF |
= |
Conversion factor =
O3/NO3¯ = 0.7742 |
Mol Vol |
= |
Molar volume (L/mol) = 24.45 (25°C and
760 mmHg) |
AV |
= |
Air volume (L) |
Mol Wt |
= |
Molecular weight for O3 =
47.997 (g/mol) | 3.8 Add the results of the first and second filters
to give one final O3 concentration. If a significant
amount of analyte (>25 % of first filter) is found on the
back-up (second) filter, breakthrough may have
occurred. Report possible breakthrough as a note on the report
form.
3.9 Report results to the industrial hygienist as ppm
O3.
4. Backup
Data
This method has been validated for 90-L, 180-min
samples taken at a flow rate of 0.5 L/min. The method validation was
conducted at different concentration levels near the OSHA TWA PEL of
0.1 ppm O3. In addition, 15-min samples were
also validated near the OSHA Final Rule STEL of 0.3 ppm. The
sampling medium used during the validation consisted of a
two-section polystyrene cassette containing two IGFFs.
The second IGFF serves as a backup filter. During collection
efficiency and breakthrough tests, two separate cassettes containing
one IGFF each per sample were used. The IGFFs were prepared as
described in Section
2.1.3. The 37-mm GFFs were obtained commercially
from Gelman Sciences (Lot no. 130404, Product no. 61652, Type A/E,
Ann Arbor, MI).
In addition, a separate experiment of a
passive monitor for O3 was conducted early in the
evaluation. The passive monitor (Ogawa & Co., USA, Inc., Pompano
Beach, FL) operates on a principle similar to the reaction used for
this active sampler. The monitor was tested to determine potential
OSHA compliance use.
The validation consisted of the
following experiments and discussion:
- An analysis of 20 spiked samples (7 samples each at 1 and 2
times, and 6 samples at 0.5 times the TWA PEL) to evaluate
analytical recovery as desorption efficiency (DE).
- A sampling and analysis of 22 samples (7 samples each at 1 and
2 times, and 8 samples at 0.5 times the TWA PEL) collected from
dynamically generated test atmospheres at 50% RH to determine bias
and overall error. Samples at a concentration near the STEL (0.3
ppm) were also taken.
- A determination of the sampling medium collection efficiency
at approximately 2 times the TWA PEL.
- A determination of potential breakthrough.
- An evaluation of storage stability at room (20-25°C
temperatures for 26 collected samples.
- A determination of any significant humidity effects during
sampling.
- A determination of the qualitative and quantitative detection
limits.
- Comparison of sampling methods - impinger vs. treated filter
vs. passive monitor (AKI vs. IGFF vs. OPS).
- Interface study.
- Shelf-life of the IGFFs.
- Summary.
A generation system was
assembled as shown in Figure
2, and used for all experiments except the analysis,
shelf-life study, and detection limit determinations.
All samples were analyzed by IC using a UV-VIS
detector. All known concentrations of generated test atmospheres
were determined using the AKI method for ozone (Ref.
5.2). All sampling tests were conducted using
side-by-side IC and AKI samples. These samples were
then analyzed using the conditions recommended in their
methods.
All results were calculated from concentration vs.
response curves and statistically examined for outliers. In
addition, the analytical recovery (Section
4.1) and sampling and analysis results (Section
4.2) were tested for homogeneity of variance. Possible outliers
were deter-mined using the Treatment of Outliers Test (Ref.
5.15). Homogeneity of variance was determined using Bartlett's
test (Ref.
5.16). Statistical evaluation was conducted according to the
Inorganic Methods Evaluation Protocol (Ref.
5.17). The overall error (OE) (Ref.
5.17) was calculated using the equation:
OEi% = ±(|biasi| + 2CVi) X 100% (at the 95%
confidence level)
Where i is
the respective sample pool being examined.
Block Diagram of the Laboratory Generation
System
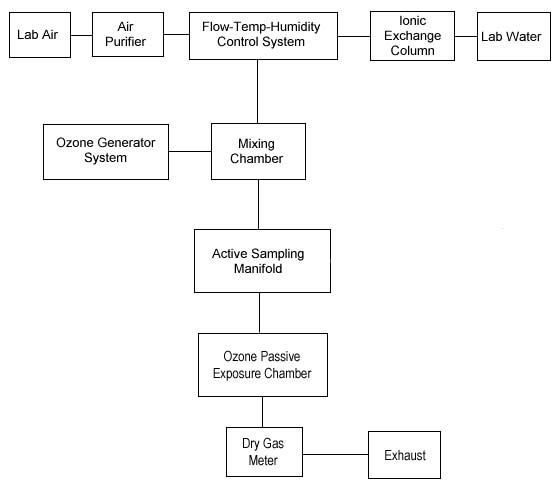 |
Figure
2 |
Text Version: Lab air
passes through an Air Purifier and then enters the
Flow-Temp-Humidity Control System. Lab Water passes through an
Ionic Exchange Column, where it is purified, and then enters
the Flow-Temp-Humidity Control System. The Flow-Temp-Humidity
Control System generates properly conditioned dilution air
that enters the Mixing Chamber. Ozone is produced by the Ozone
Generator System and it enters the Mixing Chamber to be
completely mixed with dilution air to produce the ozone test
atmosphere. The ozone test atmosphere enters the Active
Sampling Manifold. The Active Sampling Manifold provides a
means to sample the ozone atmosphere such as described in OSHA
Method ID 214. The ozone test atmosphere next enters an Ozone
Passive Exposure Chamber where diffusive samplers can be
exposed to the ozone test atmosphere. The ozone test
atmosphere next passes through a Dry Test Meter where the
total air/ozone volume is measured. Finally, the ozone test
atmosphere enters the laboratory Exhaust system and goes to
waste. |
4.1 Analytical
Recovery
Ozone oxidizes sodium nitrite to sodium
nitrate on the filter. To test the relative analytical capability
of this method, sodium nitrate was used as the analytical spike.
Twenty samples were prepared by adding known amounts of
NO3 (as NaNO3) stock solution to the IGFFs
to determine desorption efficiencies (DEs) for the analytical
portion of the method.
4.1.1 Procedure: Each IGFF
was spiked using a 25- or 50-µL syringe (Hamilton
Microliter/Gastight Syringe, Hamilton Co., Reno, NV). The IGFF
samples were inside cassettes when spiked with aqueous
solutions. Spikes were either 11.5, 23.0, and 46.0 µg
NO3¯. These levels correspond to approximately 0.5,
1, and 2 times the TWA PEL for a 90-L air sample at
a 0.5-L/min flow rate. The cassettes were allowed
to sit overnight and then analyzed.
4.1.2 Results: Desorption efficiencies are presented
in Table 1. As shown, the average DE is very close to 1.0. No DE
corrections are necessary for O3 collection using
IGFFs.
Table 1 Ozone (as NO3¯)
Analysis - Desorption Efficiency (DE)
|
level (¯) |
N |
mean DE |
SD |
CV1 |
|
0.5 × PEL 1 × PEL 2 × PEL all
levels |
6 7 7 20 |
0.979 1.025 0.977 0.994 |
0.055 0.029 0.47 - |
0.056 0.028 0.048 0.045 * |
*CV1
(pooled) | 4.2 Sampling and Analysis
To
determine the precision and accuracy of the method, known
concentrations of O3 were generated, samples were
collected, and analyzed.
4.2.1 Procedure:
- Test atmospheres of O3 were generated using two
ozone generators (Model 565, ThermoElectron Instruments,
Hopkinton, MA) simultaneously to achieve as high O3
concentrations as possible. The O3 gas was diluted
with filtered, humidified air using the system shown in Figure
2 and discussed below. A glass mixing chamber was used to
facilitate blending of ozone with the diluent air.
- Dynamic generation system
A Miller-Nelson Research
Inc. flow, temperature, and humidity control system (Model
HCS-301, Monterey, CA) was used to control and
condition the dilution airstream. All generation system
fittings and connections were Teflon. The O3
concentrations were varied by adjusting the dilution airstream
Volume. The dilution airstream was adjusted using the mass
flow controller of the Miller-Nelson system. For
this experiment, the system was set to generate test
atmospheres at 50% RH and 25°C. Test atmosphere concentrations
were approximately 0.5, 1, and 2 times the OSHA TWA PEL and at
the OSHA STEL.
- The total flow rate of the generation system was measured
using a dry test meter.
- IGFF/cassette samples were attached to the Teflon sampling
manifold using Gilian Gil-Air SC pumps (Gilian
Instrument Corp., W. Caldwell, NJ) to draw the O3
test atmosphere through the IGFF samples. Pump flow rates were
approximately 0.5 and 1.5 L/min and sampling times were 180
and 15 min for TWA and STEL experiments, respectively.
4.2.2 Results: The results are shown in Tables 2a
and 2b.
The spiked sample (Table
1) and test atmosphere sample (Table 2a) results each passed
the Bartlett's test and were pooled to determine a CVT for the
TWA sampling and analytical method.
Table 2a Ozone sampling and Analysis
- TWA PEL Determinations
|
level (¯) |
N |
ave recovery |
SD |
CV2 |
OE2 (±%) |
|
0.5 1 2 all levels |
8 7 7 22 |
1.032 1.071 0.937 1.014 |
0.060 0.023 0.028 - |
0.059 0.022 0.030
0.041* |
14.9 11.5 12.3
9.7 ** |
* CV2 (pooled) - ** OE2
(pooled) | The
total pooled coefficients of variation (CVT), bias,
and total overall error (OET) are as follows:
CVT (pooled) = 0.045 |
bias = + 0.014 |
OET =
10.4% | (Note:
The CVT and OET values include data from
Section
4.1 and are calculated using equations specified in Refs. 5.16-5.17.)
Table 2b Ozone Sampling and Analysis
- STEL PEL Determination (Known O3 Concentration
= 0.33 ppm)
|
level(¯) |
N |
mean ppm found |
SD |
CV |
recovery |
OE |
|
STEL |
5 |
0.325 |
0.018 |
0.054 |
98.5% |
±12.3% |
| 4.3 Collection Efficiency
Procedure: Seven IGFF/cassettes were used to
collect a concentration of approximately 2 times the OSHA TWA PEL
for 180 min at 0.5 L/min (50% RH and 25°C. The amounts of
O3 gas collected on the first and second IGFFs were
determined. The collection efficiency (CE) was calculated by
dividing the amount of O3 collected in the first filter
by the total amount of O3 collected in the first and
second IGFFs.
Results: The results
in Table 3 show a CE of 100%. No O3 was found in the
second IGFF for the CE experiment and indicates the IGFFs have
adequate collection of O3 near the
PEL.
Table 3 Collection Efficiency
(CE) 2 × PEL - 25°C - 50% RH
|
|
ppm O3
|
sample no. |
1st IGFF |
2nd IGFF |
CE, % |
|
1 2 3 4 5 6 7 |
0.209 0.220 0.203 0.216 0.211 0.204 0.206 |
ND ND ND ND ND ND ND |
100.0 100.0 100.0 100.0 100.0 100.0 100.0 |
|
Notes: |
(a) |
Sampled at 0.5 L/min for 180 min. |
|
(b) |
Samples desorbed using a sample solution
volume of 5.0 mL |
|
(c) |
ND = None detectable (< 0.008 ppm
O3) | 4.4 Breakthrough
(Note: Breakthrough is
defined as > 5 % loss of analyte from the first IGFF to a
backup IGFF at 50% RH)
Procedure:
The same procedure as the CE experiment (Section
4.3) was used with two exceptions: In addition to the 2 ×
concentration, the generation concentration was increased to a
level approximately 4 times the TWA PEL, and samples were taken at
approximately 0.5 L/min for 240 min. Another test was conducted
for 6 times the TWA PEL using a sampling rate of approximately
0.25 L/min for 240 min. Due to limitations on the O3
generators and the generation system, larger O3
concentrations could not be achieved.
The amount of
breakthrough for each sampling cassette was calculated by dividing
the amount collected in the second IGFF by the total amount of
O3 collected in the first and second
IGFFs.
Results: For measurements
near the TWA PEL, no breakthrough of O3 into the second
section was found at an approximate concentration of 0.2 ppm
O3 (Table 4a), and indicates the first IGFF has
adequate retention of O3 at 2 times TWA PEL. However,
the average breakthrough was 7.5% at an approximate concentration
of 0.4 ppm O3 (Table
4b) for 240 min at 0.5 L/min flow rate. No break-through was
found at the approximate concentration of 0.6 ppm O3
(Table
4c) when using a lower flow rate of 0.25 L/min. For the STEL,
no breakthrough was found at approximate concentration of 0.3 ppm
O3 (Table
4d) for 15 min at 1.5 L/min sample collection flow rate.
Table 4a Breakthrough Study - 0.5
L/min 2 × PEL - 25°C - 50% RH
|
|
ppm O3
|
sample no. |
1st IGFF |
2nd IGFF |
Breakthrough, % |
|
1 2 3 4 5 6 |
0.242 0.281 0.190 0.227 0.238 0.215 |
ND ND ND ND ND ND |
0 0 0 0 0 0 |
|
Notes: |
(a) |
Sampled at - 0.5 L/min for 240 min |
|
(b) |
Due to the larger sampling period and thus
larger mass collected, the first IGFF was desorbed using
larger sample solution volumes of 10.0 mL. |
|
(c) |
ND = None detectable (< 0.008 ppm
O3) |
Table 4b Breakthrough Study - 0.5
L/min 4 × PEL - 25°C - 50% RH
|
|
ppm O3
|
sample no. |
1st IGFF |
2nd IGFF |
CE, % |
|
1 2 3 4 5 6 |
0.425 0.385 0.395 0.363 0.383 0.342 |
ND ND ND ND ND ND |
0 0 0 0 0 0 |
|
Notes: |
(a) |
Sampled at - 0.5 L/min for 240 min |
|
(b) |
Due to the larger sampling period and thus
larger mass collected, the first IGFF was desorbed using
larger sample solution volumes of 15.0 mL. |
|
(c) |
Statistical analysis - N = 8; mean = 7.5;
SD = 1.5; CV = 0.20 |
Table 4c Breakthrough Study - 0.25
L/min 4 × PEL - 25°C - 50% RH
|
|
ppm O3
|
sample no. |
1st IGFF |
2nd IGFF |
Breakthrough, % |
|
1 2 3 4 5 6 |
0.563 0.600 0.586 0.661 0.566 0.558 |
ND ND ND ND ND ND |
0 0 0 0 0 0 |
|
Notes: |
(a) |
Sampled at - 0.25 L/min for 240 min |
|
(b) |
Due to the larger sampling period and thus
larger mass collected, the first IGFF was desorbed using
larger sample solution volumes of 10.0 mL. |
|
(c) |
ND = None detectable (<0.008 ppm
O3) |
Table 4d Breakthrough Study - 1.5
L/min 1 × PEL - 25°C - 50% RH
|
|
ppm O3
|
sample no. |
1st IGFF |
2nd IGFF |
Breakthrough, % |
|
1 2 3 4 5 6 |
0.440 0.308 0.333 0.346 0.306 0.334 |
ND ND ND ND ND ND |
0 0 0 0 0 0 |
|
Notes: |
(a) |
Sampled at - 1.5 L/min for 15 min |
|
(b) |
Samples desorbed using a sample solution
volume of 5.0 mL |
|
(c) |
ND = None detectable (< 0.032 ppm
O3) |
4.5 Storage Stability
Procedure: A study was conducted to assess the
stability of the NO2¯ + O3 reaction product,
NO3¯ on the IGFFs. A room temperature storage stability
study using 26 samples taken near the OSHA TWA PEL of 0.1 ppm was
performed. All samples were stored under normal laboratory
conditions (20-25°C) in a plastic bag in a drawer. Seven samples
were initially desorbed and analyzed; seven more samples were
desorbed and analyzed after 5 days, followed by six samples at 15,
and 30 days, respectively.
Results:
The mean of samples analyzed after 30 days was within 10% of the
mean of samples analyzed the first day, as shown in Table 5 and
Figure 3 below.
Table 5 Storage Stability -
Ozone (25°C, and 50% RH) (Known O3
Concentration = 0.123 ppm)
|
Day |
N |
Mean O3Found |
SD |
CV |
Recovery (%) |
|
1 5 15 30 |
7 7 6 6 |
0.122 0.120 0.135 0.116 |
0.005 0.004 0.002 0.006 |
0.038 0.036 0.015 0.052 |
99.2 97.6 109.8 94.3 |
|
Storage Stability
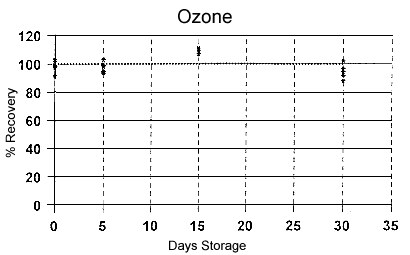
Figure 3 |
Text Version: Figure 3
is a graph of the storage stability data shown in Table 5.
The graph shows percent ozone recovery-plotted on the y-axis
against days of storage time-plotted on the x-axis.
The storage stability is excellent, with approximately 94%
of the ozone recovered after 30 days of ambient
storage. | 4.6
Humidity Study
Procedure: A study
was conducted to determine any effect on recovery results when
samples are collected at different humidities. Samples were taken
using the generation system and procedure described in Section
4.2. Test atmospheres were generated at 25°C and at
approximately 0.5, 1, and 2 times the OSHA TWA PEL. Relative
humidities of 30%, 50%, and 80% were used at each concentration
level tested.
Results: Results of
the humidity tests are listed in Table 6. An F test was used to
determine if any significant effect occurred when sampling at
different RHs. As shown, at the 99% confidence level, the
calculated F values are much smaller than critical F values (Ref.
5.16) for all the concentrations tested; therefore, no
significant difference in results occurred across the RH ranges
tested.
Table 6 Humidity Test -
Ozone 25°C
|
Level |
RH, % |
N |
Mean O3 Found |
SD |
CV |
Taken |
Recovery, % |
Fcrit |
Fcalc |
|
0.5 × PEL |
30 50 80 |
7 8 7 |
0.073 0.072 0.060 |
0.008 0.004 0.001 |
0.107 0.059 0.024 |
0.070 0.070 0.058 |
104 103 103 |
5.93 |
0.02 |
|
1 × PEL |
30 50 80 |
6 7 7 |
0.119 0.118 0.101 |
0.007 0.003 0.002 |
0.059 0.022 0.022 |
0.115 0.110 0.098 |
103 107 103 |
6.11 |
2.62 |
|
2 × PEL |
30 50 80 |
7 7 7 |
0.174 0.222 0.231 |
0.005 0.006 0.006 |
0.030 0.028 0.027 |
0.172 0.224 0.237 |
101 99.1 97.5 |
6.01 |
2.71 |
| 4.7 Qualitative
and Quantitative Detection Limit Study
A modification of
the National Institute for Occupational Safety and Health (NIOSH)
detection limit calculations (Refs. 5.18-5.19)
was used to calculate detection limits.
Procedure: Low concentration samples were
prepared by spiking aqueous standards prepared from
NaNO3 (Section
3.3.4) at five different concentrations on the IGFFs. Samples
were analyzed using a 50-µL sample injection loop and a UV-VIS
detector setting of 2 AUFS.
Results: The IGFF spiked sample results are
shown in Table 7 for qualitative and quantitative detection
limits, respectively. The qualitative detection limit is 0.37
µg/mL as NO3¯ at the 99.8% confidence level. The
quantitative detection limit is 1.25 µg/mL as NO3¯.
Using a 90-L air volume and a 5-mL
sample solution volume, the qualitative and quantitative detection
limits are 0.008 ppm and 0.03 ppm, respectively, as O3.
Table 7 Qualitative and Quantitative
Detection Limits (NIOSH Method)
|
|
O3 (as
NO3¯) Level
|
Sample No. |
Blank PA |
0.1 µg/mL PA |
0.2 µg/mL PA |
0.5 µg/mL PA |
1.0 µg/mL PA |
|
1 2 3 4 5 6 |
2.05 1.98 2.02 2.03 2.02 1.74* |
2.73 2.60 1.81* 2.60 2.68 2.69 |
2.25 3.15 3.15 3.23 4.55* 3.79 |
3.17 4.15 3.21 4.09 4.12 3.24 |
5.87 4.99 4.98 5.76 5.81 5.81 |
|
* Outlier PA -
Integrated Peak Area
(NO3¯)/100,000 | The average responses of the low-level calibration
samples were plotted to obtain the linear regression equation (Y =
mX + b), and the predicted responses ( i)
at each X.
Using the equations:
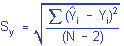 |
|
Q2 =
(3.33)Q1 |
Text Version: First
subtract each obtained response from its predicted response,
and then square that difference. Sum all these
values. Divide the sum by the number of data points
minus two. Take the square root of that value.
The result is the standard error of the regression
line. |
Therefore, |
Q1 |
= |
(3Sy)/m = 0.37 µg/mL as
NO3¯ |
|
|
 |
1.85 µg as NO3¯ (5-mL sample
volume) |
|
|
 |
0.008 ppm O3 (90-L air
volume) |
|
Q2 |
= |
(3.33)Q1 |
|
|
 |
0.027 ppm O3 (90-L air
volume) |
where: |
|
B |
= |
mean blank response |
b |
= |
intercept of the regression |
m |
= |
analytical sensitivity or slope as
calculated by linear regression |
SY |
= |
standard error of the regression =
0.21667 |
N |
= |
number of data points |
Q1 |
= |
qualitative detection limit |
Q2 |
= |
quantitative detection
limit | The
Correlation Coefficient (r) and Coefficient of Determination
(r2) for the above data were r = 0.986 and
r2 = 0. 972.
4.8 Comparison of Sampling
Methods
This method was compared with the classical AKI
approach and a passive monitor method. The Ogawa passive sampler
(OPS), developed by the Harvard School of Public Health (HSPH),
was originally designed to sample for nitrogen oxides in the
environment. Modifications allowed its use to monitor ambient
environmental ozone. The reaction principle and analysis are
similar to this lGFF method; however, the impregnating solution is
slightly different (and proprietary for the passive system), and
the samples are analyzed by IC for nitrate ion using conductivity
detection instead of UV-VIS Prior to using the OPS method for this
comparison, the sampling rate was examined. Due to face velocity
dependence, sampling rates are critical to the performance of the
passive monitor during this comparison. The determination of
sampling rate is detailed in the Appendix.
Procedure: In order to compare performance, the
IGFF/cassettes (this study), AKI samples, and OPSs were collected
side by side from the generation system at approximately 0.5, 1
and 2 times the PEL. The IGFF/cassettes and OPSs were analyzed by
IC. The AKI samples were analyzed by a colorimetric procedure
further described in Ref.
5.2. The average sampling rate as determined by SLTC for the
face velocity achieved, 21.93 cm3/min, was used for
OPSs.
Results: Table 8 shows the
results of the comparison study. As shown, the IGFF/cassettes, the
AKI samples, and OPSs are in good agreement except that OPSs are
slightly higher for 1 times and lower for 2 times
PEL.
Table 8 Comparison of Methods
(Summary) (25°C and 50% RH)
|
Set # |
Method |
O3 Found, ppm |
N |
SD |
CV |
|
1 |
AKI IGFF OPS |
0.070 0.072 0.073 |
3 8 4 |
0.006 0.004 0.003 |
0.086 0.056 0.041 |
2 |
AKI IGFF OPS |
0.110 0.118 0.129 |
3 7 7 |
0.002 0.003 0.017 |
0.018 0.025 0.132 |
3 |
AKI IGFF OPS |
0.224 0.210 0.187 |
3 7 7 |
0.008 0.006 0.012 |
0.036 0.029 0.064 |
|
where: |
AKI Alkaline potassium iodide
(Ref.
5.2) |
|
IGFF Impregnated glass fiber
filter (this study) |
|
OPS Ogawa passive sample for
ozone (Refs. 5.10
and 5.20) |
NOTE: Although the passive monitor performed
reasonably well during the comparison, detection limit calculations
indicate potential problems may be incurred for OSHA compliance use.
The monitor was originally designed for environmental
(24-h) use. Using the manufacturer's stated detection
limit of 200 ppb-h as analyzed using IC and a
conductivity detector (the manufacturer's recommended analytical
technique), an 8-h detection limit of 0.025 ppm would
be obtained (using a UV-VIS detector SLTC indicates a quantitative
detection limit of about 0.1 ppm-h; however, for STEL
or intermittent sampling the monitor still appears not sufficiently
sensitive). This would necessitate 7 to 8-h sampling
and would not be ' conducive to STEL or intermittent sampling
occasionally required in monitoring situations. The monitor appears
beneficial in industrial hygiene situations provided large
concentrations ( > 0.1 to 0.2 ppm O3) are present or 7
to 8-h sampling is performed. The study to determine
applicability was halted after preliminary determinations indicated
the passive monitor also suffered from the same negative
interference from SO2 as the active sampler ( Section
4.9). In a recent paper (Ref.
5.10), the authors indicated that SO2 should not
interfere with the passive sampler collection of O3;
however, experiments to verify this were not presented in the
paper.
4.9 Interference
Study
As previously discussed in Section
1., oxidizing gases have interfered with the determination of
O3 in previous methods (Refs. 5.1-5.2,
5.4).
Several tests were conducted to evaluate any possible interference
from NO2 or SO2.
Procedure: Possible interferences from
NO2 and SO2 were tested using several sets
of IGFF/cassette samples. A test was conducted by taking four
samples at approximately 6 ppm NO2 and compared to four
samples without NO2 which served as "control" samples.
Several tests were conducted to evaluate any SO2
interference by comparing results of six samples with
SO2 to another four to six samples without
SO2, present. These tests included two different
SO2 concentrations and use of oxidizer tubes for
removal of SO2 from the sampled air prior to
O3 reaction with the treated filters.
Two
different kinds of oxidizer tubes were evaluated. Both were
manufactured by SKC Inc. (Eighty Four, PA) and are used to convert
nitric oxide (NO) to nitrogen dioxide (NO2) during
sampling for NO. The two types of oxidizer tubes
are:
Tube Label
|
Substrate
|
Abbrev.
|
Oxidizer Special |
Chromate impregnated sand |
OS |
Misc-Spec |
Chromate impregnated
material (Composition of substrate unknown) |
MS | Both tube labels are designations given by SKC.
Chromate impregnated sorbent has been shown to effectively remove
SO2 during ozone sampling (Ref.
5.21). All samples were taken at a flow rate of about 0.5
L/min for 180 min. The generation system concentration was
approximately 1.5 times the TWA PEL for ozone.
Results: Table 9 shows the results of the
IGFF/cassette sample sets:
Sample Set No.
|
Description
|
1) |
O3 with and without
NO2 |
2) |
O3 with and without
SO2 (3.41 ppm) |
3) |
O3 with and without
SO2 (1.06 ppm) |
4) |
O3 with and without
SO2 (0.35 ppm) |
5) |
O3 + SO2 with and
without OS oxidizer |
6) |
O3 + SO2 with OS
oxidizer before and after conditioning |
7) |
O3 + SO2 with and
without MS oxidizer |
8) |
O3 + SO2 with MS
oxidizer before and after conditioning |
9) |
Comparison study between 50% and 80% RH
for O3 +SO2 with MS oxidizer after
conditioning. |
Note: Oxidizer tube conditioning is based on the
procedure discussed in Section
2.
Table 9 Interference Study -
Ozone (25°C - 50% RH and 1.5 ×PEL)
|
Sample Set # |
Interferant Concn, ppm |
Oxidizer (Yes or No) |
Conditioning (Yes or No) |
N # |
Mean O3, ppm |
SD O3, ppm |
CV% |
|
1 |
NO2, 6.38 NO2, 0 |
No NA |
NA NA |
4 4 |
0.129 0.134 |
0.007 0.003 |
5.5 20. |
2 |
SO2, 3.41 SO2, 0 |
No NA |
NA NA |
6 6 |
ND 0.168 |
- 0.009 |
- 5.5 |
3 |
SO2, 1.06 SO2, 0 |
No NA |
NA NA |
6 6 |
ND 0.169 |
- 0.013 |
- 7.8 |
4 |
SO2, 0.35 SO2, 0 |
No NA |
NA NA |
6 6 |
ND 0.169 |
- 0.013 |
- 7.8 |
5 |
SO2, 1.06 SO2, 0 |
Yes NA |
Yes NA |
6 6 |
0.141 0.142 |
0.009 0.009 |
6.3 6.0 |
6 |
SO2, 1.06 SO2,
1.06 |
Yes Yes |
No NA |
6 6 |
0.108 0.141 |
0.012 0.009 |
10.7 6.3 |
7 |
SO2, 1.06 SO2, 0 |
Yes NA |
Yes NA |
6 4 |
0.153 0.154 |
0.005 0.001 |
3.1 0.9 |
8 |
SO2, 1.06 SO2,
1.06 |
Yes Yes |
No NA |
6 6 |
0.141 0.153 |
0.014 0.005 |
9.6 3.1 |
9 |
SO2, 1.06 SO2, 1.06
* |
Yes Yes |
Yes Yes |
6 5 |
0.153 0.145 |
0.005 0.008 |
3.1 5.8 |
|
* 80% RH was used instead of
50% |
Notes: |
(a) |
NA = Not applicable |
|
(b) |
ND = None detectable (< 0.008 ppm
03) |
|
(c) |
Flow Rate = 0.5 L/min |
|
(d) |
Sample Solution Volume for Desorption =
5.0 mL |
|
(e) |
All oxidizers were conditioned for 4 h at
a concentration of approximately 0.1 ppm
O3 | As
shown in Sample Set #1, 6.38 ppm NO2 caused no
interference when sampling at 1.5 times TWA PEL ozone. When
SO2 is present along with ozone, a negative
interference equal to 100% of an equimolar concentration of ozone
is noted as shown in Sample Sets #2, #3 and #4. Sample Sets #5 and
#7 show no interference occurs when using the oxidizer tubes.
Sample Sets #6 and #8 show the difference in recovery when using
conditioned and unconditioned oxidizer tubes. As shown, the
oxidizer gave results about 23% lower when it was not conditioned
(0.108 vs. 0.141 ppm O3 when conditioned). Although.
the recoveries improved for the MS oxidizer without conditioning
(0.141 vs. 0.153 ppm when conditioned), they were still low and it
is recommended to passivate either type of oxidizer tube. Sample
Set #9 shows no significant difference in O3 recovery
when SO2 is present at 50% and 80% RH.
An
additional test was conducted to determine if the passive monitor
would be adversely affected by SO2 in a similar fashion
as the active sampler. Side-by-side active and
passive samples were taken while varying the amount of
SO2. Both passive and active samples were prepared
using the procedure stated in this method for IGFFs. (Section
2.1) Additional passive samplers were also purchased from
Ogawa; the procedure, type, and amount of chemicals used in their
treatment preparation is unknown.
As shown in Table 10, the
passive monitor, regardless of treatment in-house or from Ogawa,
appears to display the same SO2 interference as the
active sampler. Detection limits are similar to what is stated
earlier for both active and passive samplers.
Table 10 Active vs. Passive Sampler -
SO2 Interference
|
Sample Set # |
Active or Passive |
Interferant, SO2 Concn
(ppm) |
N # |
Mean O3, ppm |
SD O3, ppm |
CV % |
|
1 1 1 1 2 2 2 2 |
Active Active Passive Passive Active Active Passive Passive |
0 1.89 0 1.89 0 1.89 0 1.89 |
4 3 6 6 2 3 6 6 |
0.164 ND 0.167 ND 0.132 ND 0.130 ND |
0.006 - 0.017 - 0.007 - 0.012 - |
3.5 - 10.1 - 0.5 - 9.0 - |
|
Note: |
N = number of samples
taken. |
|
Sample Set #1 represents passive
samplers prepared using 13-mm glass fiber filters prepared
as stated in Section
2.1. |
|
Sample Set #2 represents passive
samplers purchased from Ogawa. |
|
Sets 1 and 2 used identical
Ogawa sample holders. | 4.10 Shelf Life of the
IGFFs
Thirty-nine IGFFs were prepared according to the
procedure described in Section
2.1.3 to determine the potential shelf-life of
the nitrite-impregnated filters. Previous reports
indicate the Ogawa passive monitors have a conservative shelf-life
due to aging of four weeks. The manufacturer indicates an
8-week life-span can be used if
necessary and appropriate blank corrections are performed. The
aging, or eventual conversion to nitrate appears to be facilitated
by oxygen and small amounts of ozone in the atmosphere. The
passive monitors use a reaction principle similar to the active
sampling filters in this method. For this active sampling method,
the extent of nitrite conversion to nitrate on stored filters was
used to indicate stability and was measured over a period of up to
58 days.
Procedure: Four tests were
conducted to assess IGFF shelf life:
Set 1) |
The first test was performed using 15
IGFFs which were stored in a clean and sealed plastic bag
after preparation. Five IGFFs were initially taken and
served as "control" IGFFs, desorbed with DI H2O
and analyzed for total nitrite using peak area; then six
IGFFs were desorbed and analyzed after 22 days; finally, the
remaining four IGFFs were desorbed and analyzed after a
45-day storage. |
Set 2) |
A second test was conducted with ten more
filters; six were analyzed after 6 days, and four filters
analyzed after 28 days. |
Set 3) |
A third test was performed using 11 IGFFs
which were placed in cassettes. The cassettes were then
sealed with gel bands and plastic plugs, and stored in a
clean and sealed plastic bag after
preparation. |
Set 4) |
This set of four filters was prepared
similar to the third set; however, this set was used to
assess ability to collect samples after storage. Three of
the IGFF/cassettes were used to collect O3 vapor
(0.15 ppm O3) after 58 days of
storage. | Results: Results are listed in Table 11 and
further discussed below:
Set 1) |
The conversion of nitrite to nitrate does
not significantly occur under the storage conditions
specified above for a period of approximately
20-30 days. After 45 days, conversion appears
evident. The mean peak area of the IGFFs analyzed after 22
days was only a 9% increase over the Day 0 value and almost
a 50%increase after a 45-day
storage. |
Set 2) |
The mean of the IGFFs analyzed after 28
days was only a 2% increase over the value of Day
6. |
Set 3) |
The mean of the IGFFs analyzed after 57
days was a 23 % increase over the value of Day
0. |
Set 4) |
After blank correction and 58-day storage,
the mean recovery of the O3 collected was 95.5%.
Mean O3 found was 0.143 ppm after blank IGFF
correction, and 4.0% CV. |
Table 11 Shelf-Life Test of
IGFF
|
Sample Set # |
Day i |
N # |
Mean * ×105 |
SD ×105 |
CV % |
Ratio Xi/X0 |
|
1 2
3** |
0 22 45 6 28 0 57 |
5 6 4 6 4 6 5 |
2.02 2.20 2.93 2.33 2.37 4.71 5.30 |
0.025 0.080 0.100 0.200 0.091 0.740 1.180 |
1.3 3.7 3.5 8.6 3.8 15.7 22.2 |
1.00 1.09 1.45 1.00 1.02 1.00 1.23 |
|
* |
Peak area. |
Xi/Xo |
Ratio of IGFFs (mean peak area
of Day 1 compared to that of mean Day 0). |
** |
IGFFs were placed and stored in
cassettes, scaled with scaling bands and plastic
plugs. | 4.11
Summary
The validation results indicate the method meets
both the OSHA criteria for accuracy and precision ( Ref.
5.17). The performance during collection efficiency, storage
stability, and humidity tests is adequate. For the breakthrough
study, it appears that 7.5% breakthrough occurs onto a second IGFF
at a concentration of 0.4 ppm O3 at 0.5 L/min for 240
min. Although the second filter effectively captures the analyte
at 0.4 ppm, precautions should be taken at higher concentrations.
For O3 concentrations above 0.4 ppm, a flow rate of
0.25 L/min can be used. Breakthrough is not evident at lower
concentrations; however, the second IGFF should always be analyzed
to assure capture of all analyte. Experiments above approximately
0.6 ppm using a sample collection rate of 0.25 L/min were not
performed due to limitations in the test atmosphere generation
system. Detection limits (as NO3¯) are adequate when
samples are taken for 180 min at 0.5 L/min. The conversion of
nitrite on the IGFFs appears limited up to 28 days after
impregnating if the 2 treated filters are stored in a clean,
sealed plastic bag.
The mechanism of the
SO2/O3 interference which diminishes the
O3 conversion of nitrite to nitrate is unknown. Using
the AED-030 (semiconductor sensor)
direct-reading instrument side-by-side
with the IGFFs while sampling an SO2/O3
atmosphere, a corresponding loss of O3 was not noted.
The ability of glass fiber filters to capture and convert
SO2, due primarily to their slightly basic nature, was
previously noted in OSHA Method ID-200 for sulfur
dioxide. It has been reported in the literature (Ref.
5.22) that the chemistry of SO2 in ambient air and
on surfaces is complex. Fortunately, an oxidizer tube appears to
completely remove SO2 from the sampled stream.
Presumably the SO2 can react with any ozone or oxygen
in the presence of nitrite (and possibly glass fiber filters) to
form sulfite and eventually sulfate. No significant increase in
the sulfate content over background amounts was noted in the
chromatograms of IGFF samples taken after using oxidizer tubes to
sample an SO2/O3 atmosphere. For samples
taken in the SO2/O3 atmosphere without
oxidizer tubes, a significant increase in sulfate content was
noted from the resultant oxidation of SO2. The
SO2 interference appears to be a sampling phenomena
occurring at the surface of the IGFFs and is not dependent on
analysis. Other environmental pollutants which could potentially
adversely affect this ozone sampling method have been considered
in the literature. For example, nitric acid vapor, if present,
could be collected on the IGFFs during sampling. However, under
typical ambient conditions this positive interference probably
represents less than 5% of the nitrate formed during the
nitrite/ozone reaction (Ref.
5.23). Further study may be needed to determine other oxidized
or reduced compounds which may coexist with O3 and
cause either positive or negative interferences, such as
peroxyacetyl nitrate (PAN), a strong oxidant, which could oxidize
nitrite to nitrate. Since ambient concentrations of PAN are
typically 10-20 times smaller than ozone
concentrations, significant interference in most locations is not
expected (Ref.
5.24).
This method was validated using a UV-VIS
detector. A conductivity detector was used to assess potential
interference byproducts such as sulfite/sulfate concentrations.
Prior to completion of the method another chemist was given
approximately 25 field samples to analyze and indicate any
problems that may occur during routine analysis. Sample
concentrations covered a wide range and were analyzed both by UV
and conductivity detection. A difference in ozone results was not
noted between the two detectors. Either detector should have
adequate sensitivity and capability. The IC conductivity detector
has been used for nitrate determination since its inception over
15 years ago. The UV detection technique may be less prone to
interferences because of the greater selectivity (wavelength
specificity) for each analyte. More crucial to analysis is the
ability to separate the nitrite and nitrate peaks using
appropriate columns. Precautions should be taken to assure
adequate separation prior to sample analysis regardless of which
detector is used. 5.
References
5.1 U.S.
Environmental Protection Agency: Evaluation of I Percent Neutral
Buffered Potassium Iodide Procedure for
Calibration of Ozone Monitors by M. E. Beard, J. H.
Margeson, and E. C. Ellis (EPA-600/4-77-005).
Environmental Monitoring Series. Research Triangle Park.
N.C., 1977.
5.2 National Institute for
Occupational Safety and Health: Documentation of the NIOSH Validation Tests by D. Taylor, R. Kupel and ".
Bryant (DHEW-NIOSH publication No. 77-185). NIOSH
Analytical Methods for Standard Completion Program (Method No. S8
- Ozone). Washington, D.C.: U.S. Government Printing Office,
1977.
5.3 Hekmat, M., P. Fung, and R.
Smith: Instability of Ozone Samples Collected in Alkaline
Potassium Iodide Solution. Am Ind. Hyg.
Assoc. J. 53: 672 (1992).
5.4
Occupational Safety and Health Administration Salt Lake Technical
Center: Ozone (KIBRT) in Workplace
Atmospheres (USDOL/OSHA-SLCAL Method No.
ID-150). Salt Lake City, UT: Occupational Safety and
Health Administration Salt Lake Technical Center, 1984.
5.5 Occupational Safety and Health Administration
Salt Lake Technical Center: Ozone (Stilbene) in
Workplace Atmospheres (USDOL/OSHA-SLCAL Method
No. ID-209). Salt Lake City, UT: Occupational Safety
and Health Administration Salt Lake Technical Center, 1990
unpublished.
5.6 Sawatari, K.: Personal
Dosimeter for Ozone using the Ozonolysis of
Trans-stilbene. Industrial Health
22: 117-126 (1984).
5.7 Ku,
J.C.: Private Notes, 1989.
5.8 Analytical Instrumental Development Inc.:
Ozone Portable Analyzer. Model 560, Technical
Document. Avondale, PA: Analytical Instrumental Development
Inc., 1980.
5.9 In USA Inc.: Ozone Hunter, AET - 030. Technical Document.
Newtonville, MA: In USA Inc., 1992.
5.10 Koutrakis, P., J.M. Wolfson, A.
Bunyaviroch, S.E. Froehlich, K. Hirano and J.D. Mulik: Measurement
of Ambient Ozone Using a Nitrite-Coated Filter. Anal. Chem. 65: 209-214(1993).
5.11 Hawley, G.G.: The
Condensed Chemical Dictionary. I 11th ed. New York: Van
Nostrand Reinhold Co., 1987.
5.12
American Society for Testing and Materials (ASTM): Standard Practice for Safety and Health Requirements
Relating to Occupational Exposure to Ozone
(E591-80). In 1988 Annual Book of ASTM
Standards, Section H, Volume 11.03, Philadelphia, PA: ASTM, 1988.
pp. 411-439.
5.13 "Ozone"
Federal Register 54:12 (19 Jan. 1989). pp.
2519-2520.
5.14
Occupational Safety and Health Administration Salt Lake Technical
Center: Ion Chromatography Standard Operating
Procedure (Ion Chromatographic Committee). Salt Lake City,
UT: Occupational Safety and Health Administration Salt Lake
Technical Center, in progress.
5.15
Mandel, J.: Accuracy and Precision, Evaluation and Interpretation
of Analytical Results, The Treatment of Outliers. In Treatise On Analytical Chemistry. 2nd ed.,
Vol. 1, edited by 1. M. Kolthoff and P. J. Elving. New York, NY:
John Wiley and Sons, 1978. pp. 282-285.
5.16 National Institute for Occupational Safety
and Health: Documentation of the NIOSH
Validation Tests by D. Taylor, R. Kupel, and J. Bryant
(DHEW/NIOSH Pub. No. 77-185). Cincinnati, OH:
National Institute for Occupational Safety and Health, 1977. pp.
1-12.
5.17 Occupational
Safety and Health Administration Salt Lake Technical Center:
Evaluation Guidelines of the Inorganic Methods Branch. In OSHA
Analytical Methods Manual. 2nd ed.
Cincinnati, OH: American Conference of Governmental Industrial
Hygienists, 1991. pp. I18.
5.18
Burkart, J.A.: General Procedures for Limit of Detection
Calculations in the Industrial Hygiene Chemistry Laboratory. Appl.
Ind. Hyg. 1:
153-155(1986).
5.19 National Institute for Occupational Safety
and Health: Standard Operating Procedures for
Industrial Hygiene Sampling and Chemical Analysis, SOP 018,
Cincinnati, OH: National Institute for Occupational Safety and
Health, Revised Sept., 1992.
5.20
Ogawa & Co., USA, Inc.: The Ogawa Passive
Sampler for Ozone Operation Manual. Pompano Beach, FL:
Ogawa & Co., USA, Inc., 1993.
5.21
Committee on Medical and Biologic Effects of Environmental
Pollutants: Ozone and Other Photochemical
Oxidants. National Academy of Sciences, Washington, D.C.,
1977. p. 264.
5.22 Chang, D.P.Y.:
Sulfur Compounds ' in Ambient Environments and Their Simulation in
the Laboratory. Generation of Aerosols and
Facilities for Exposure Experiments edited by K.Willeke.
Ann Arbor, MI: Ann Arbor Science Publishers, Inc., 1980. p.
302-304.
5.23 Koutrakis,
P., P. Mueller: Paper No. 89-71.4. In Proceedings of
the 82nd Annual Meeting of the Air and Waste Management
Association, 1989.
5.24
Finlayson-Pitts, B. and J.N. Pitts: Atmospheric
Chemistry, New York, NY: John Wiley &Sons, 1986.
Appendix
Sampling Rate - Ogawa Passive
Samplers for Ozone | The OSHA-SLTC was interested in examining performance
of the passive monitor for potential OSHA compliance use. The
sampling simplicity of the monitor is very attractive to compliance
officers, and the possibility of offering both active and passive
samplers for O3 was explored. To verify the passive
monitor sampling rate, the mass collected by the passive sampler
when exposed to various concentrations of ozone was
measured.
Procedure: A "known"
concentration was determined from the IGFF method and confirmed by
the AKI method. The OPSs, IGFFs, and AKI samples were collected
side-by-side from the generation system at
approximately 0.5, 1, and 2 times PEL. The passive monitors were
placed in a 1-L buret (area section = 19.63
cm2 or 0.021 ft2), and the open end of the
buret was sealed with a cork stopper. This exposure chamber was in
series with a Teflon sampling manifold where the active samplers
were collected. The face velocity (air movement in front of the
passive monitor) was 8.3 ft/min. The low face velocity was necessary
due to dependence on the generation system design and concentrations
generated. The sampling rate must be determined if this face
velocity is used in method comparisons. The manufacturer's stated
rate of 18.1 cm3/min is for higher face velocities.
Normal face velocities in general industry typically range from 25
to 100 ft/min. The sampling time was 480 min. Sampling for the
passive monitors was conducted according to the OPS instruction
manual (Ref.
5.20).
Results: The Table below
shows the calculated sampling rates at the different O3
concentrations. The sampling rate was calculated based on diffusion
theory. A more detailed description about diffusion theory (Fick's
First Law of Diffusion) and specific application can be found
elsewhere (e.g., Ref.
5.10). As shown, the average sampling rate is 21.93 ± 2.28
cm3/min. Note that this rate lies between the
theoretically predicted rate, 24.5 cm3/min and the
observed value, 18.1 ± 1.9 cm3/min reported by HSPH (Ref.
5.10).
Sampling Rate Validation for Ogawa Ozone
Passive Samplers (25°C - 50% RH - 8.3 ft/min Face Velocity* and
480-min Sampling Time)
|
Level |
O3 Concn ppm |
Mean O3 Mass Found, µg |
N # |
Mean Sampling Rate**,
cm3/min |
SD cm3/min |
CV % |
|
0.5 × PEL 1 × PEL 2 × PEL |
0.072 0.118 0.210 |
1.507 2.676 3.864 |
4 7 7 |
22.22 24.06 19.52 |
0.95 3.39 1.33 |
4.3 14.1 6.8 |
|
Average Sampling Rate = 21.93 ±
2.28 cm3/min |
* |
Calculated from 1-L buret used as an
exposure chamber (area section = 19.63 cm2 or 0.021
ft2) and test atmosphere flow rate of 5 L/min
through the chamber. |
** |
Values calculated based on the following
equation: |
Sampling Rate ( |
cc
min |
) = |
O3 found (µg) × 24.46 × 1000
O3 Conc (ppm) × 47.997 × Sampling time (min)
|
where: |
O3 found (ug) = ug/mL,
NO3 × sampling volume, mL X GF |
|
03 found (ug) = ug/mL,
NO3 × 1.9355*** |
|
***If sampling volume = 2.5 mL and GF =
Gravimetric factor = 48/62 = 0.7742 are used |
|
24.46 = Molar volume at 25°C and 760
mmHg |
|
47.997 = Molecular weight of
ozone | |
|
| |